Multi Column Distillation Plant
Operation : The pre-heated feed water (through condenser) is fed into the first column where 33% of feed water is converted into steam under pressure by outside boiler steam. The pure steam produced in the first column having temperature of 135’c and the remaining feed water goes to the 2nd column. The pure steam is used as a heating media in the 2nd column and converts part of remaining feed water into steam. In the process the steam itself condenses back into water. This process is repeated till the last columns each working at low temperature & pressure as compared to the one before it. The steam produced in the last column is condensed in the condenser by feed water as well as cooling water. As external heat is required only to convert the 33% of feed water, the heating energy required is reduced by 67%. Salient Features :
- Compact unit, easy to maintain and operate.
- Total energy saving is 75% as less heating energy and less cooling water is required.
- Pyrogens are removed by centrifugal force developed & specially designed spiral baffle.
- Maintenance cost is low as there are no moving parts.
- Trouble free performance of multi-stage pump(horizontal)
- Provided with Compact control panel board.
- All contact parts are s.s.316 quality. All pipes and tubes are seamless and gaskets made form teflon.
- Distillate Temperature is quite high.( 90-95′)
- Distilled water as per IP/BP standards and conductivity less than 1 micromhos/cm.
Scope of supply Includes :
- A S.S..316 quality surge tank with float valve to maintain water level.
- Feed Water Pump s.s 316
- GRUNDFOS pump.
- Control panel board with indicating Lamps.
Technical specifications: Industrial steam at 3 bar pressure Industrial steam at 8 bar pressure
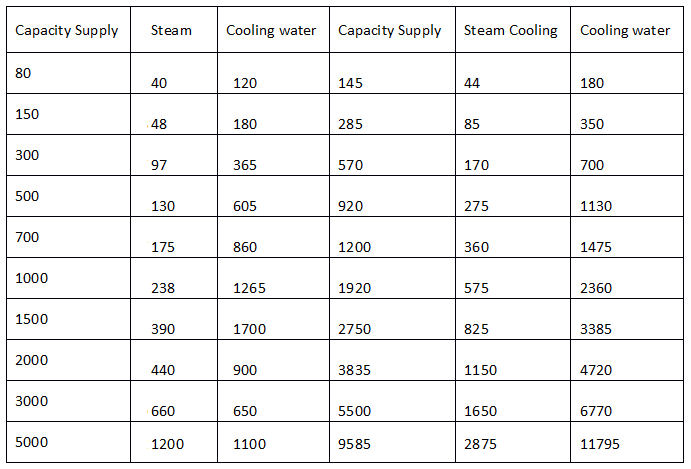